砂型鑄造是將熔煉金屬注入砂型中生產鑄件的方法,具有材料易得、生產周期短等特點,廣泛應用于汽車、新能源等行業復雜零部件的生產制造環節。由于砂型鑄造工藝復雜、作業強度大、生產標準高,許多企業也開始進行自動化改造,并引入3D視覺提升產線智能化、柔性化水平。
某頭部汽車零配件廠發動機缸體鑄造車間引入梅卡曼德3D視覺方案后,實現砂型鑄造過程中砂芯浸涂、鉆孔、組芯等工藝自動化,大幅提升企業鑄件生產效率及質量。
工藝及改造原因
01?工藝介紹
砂芯在砂型鑄造中主要用來形成鑄件內腔。制作過程較為復雜,涉及了制芯、浸涂、鉆孔、組芯等工藝。
· 制芯:將原砂、粘結劑按照一定比例混合,注入砂箱形成砂芯。
· 浸涂:在砂芯表面涂料,以提高砂芯耐火度、降低鑄件表面粗糙度、防止鑄件產生缺陷。
·?鉆孔:使砂芯排氣通暢,避免高溫金屬液注入砂芯時形成入侵氣孔,影響鑄件質量。
·?組芯:將砂芯依照裝配特征高精度組裝,形成完整且精密的鑄件內腔。
02?改造原因
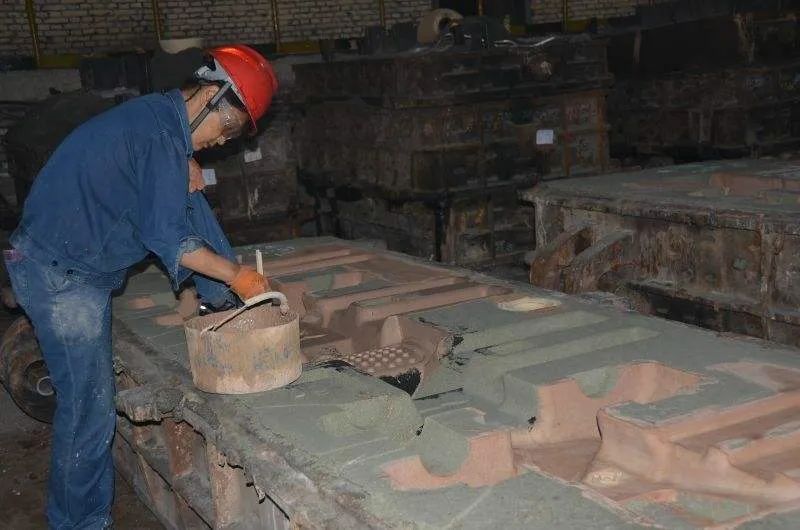
浸涂環節:人工涂覆(圖片來源自網絡)
現場有三種砂芯:機體芯、上蓋芯,下蓋芯,每種砂芯包含十數種型號。在浸涂工位,需將砂芯從輸送線搬運至浸涂池進行浸涂處理,涂料風干后,由輸送線運送至鉆孔工位鉆孔,而后轉運至下料臺。同時,需將上蓋芯和下蓋芯精準對位組裝。客戶生產過程存在以下痛點,決定對產線進行自動化改造:
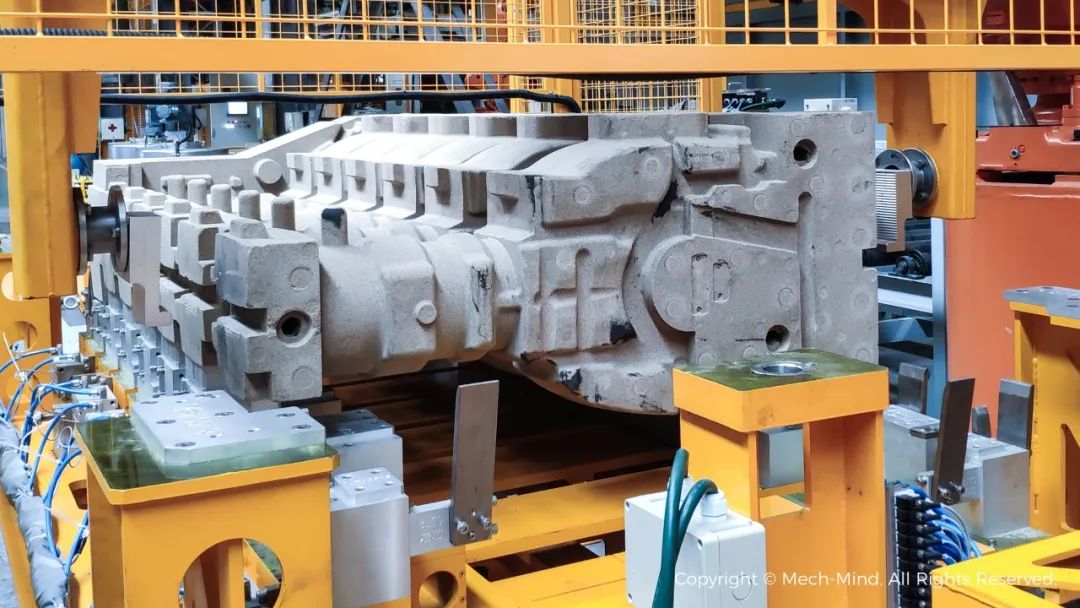
砂芯來料
·?人工涂覆效率低,易出現滴痕、刷痕等缺陷。傳統機械設備難以對砂芯精準定位,造成涂料覆蓋不均。
·?人工鉆孔一致性差,傳統機械設備鉆孔精度低。易出現錯扎、漏扎等情況,影響砂芯氣密性,導致鑄件成品出現氣孔缺陷。
·?砂芯組芯精度要求高,人工或傳統機械設備裝配精度難以滿足客戶生產需求。
·?砂芯尺寸大(可達1152×464×227mm),自重大(可達200kg),人工搬運強度大,存在危險性。
·?受鑄件自重大、高溫、粉塵、煙氣等因素影響,人工作業效率不穩定且存在健康風險。
01?解決方案

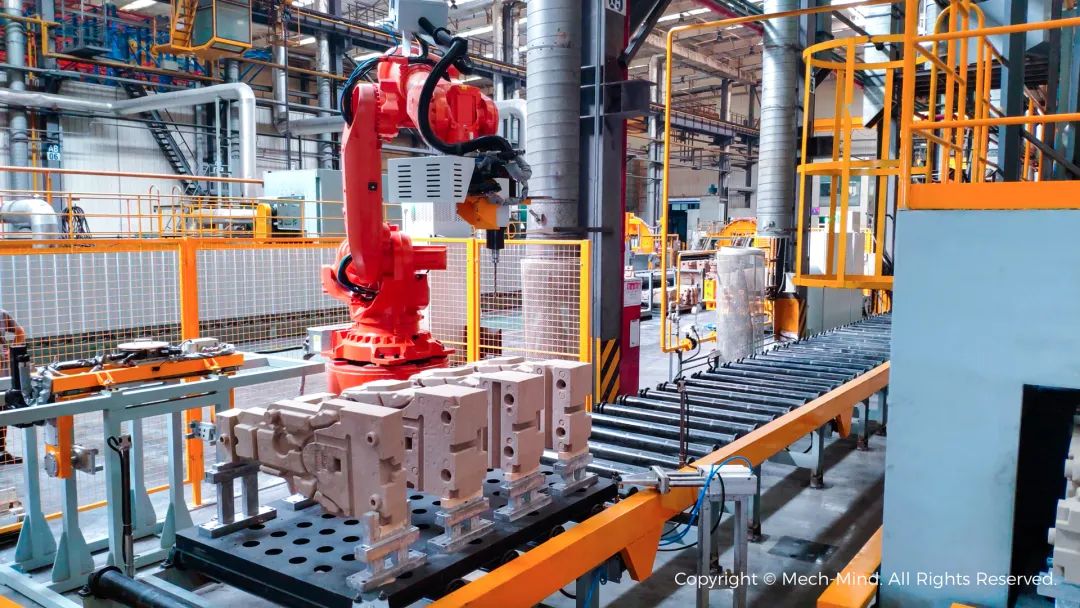
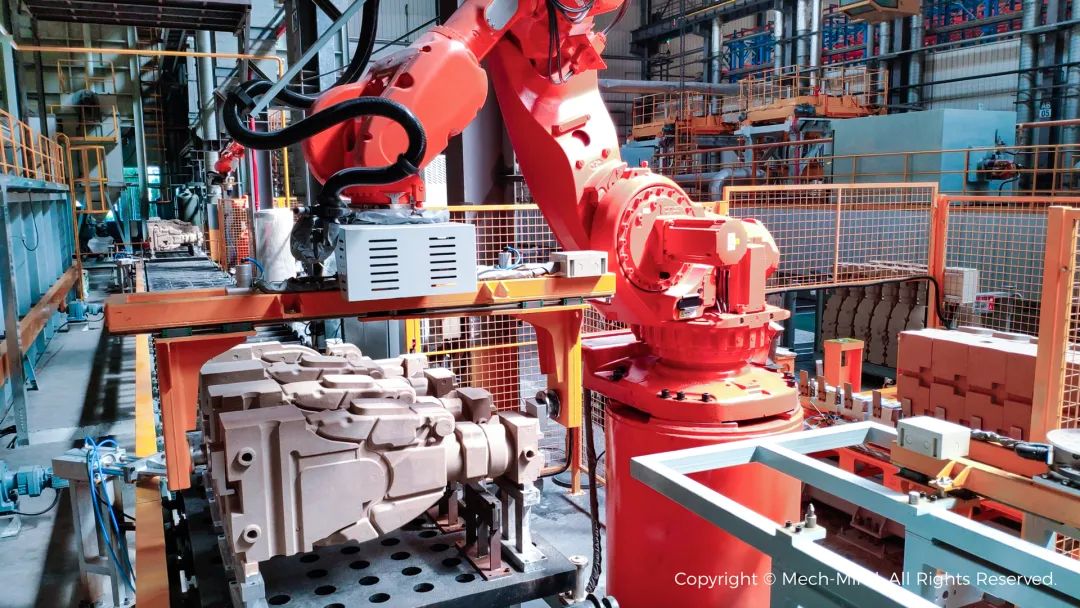
以上為項目現場圖片
3D相機選型及安裝方式:Mech-Eye PRO S,臂載式安裝。
通訊方式:3D視覺系統與機器人直接通信,通訊協議為TCP/IP。
來料方式:2-4個砂芯為一組,由托盤運輸到位。
工作流程:
·?輸送線通過托盤輸送機體芯/上蓋芯/下蓋芯至指定位置;3D相機拍照,3D視覺系統獲取待抓取砂芯位姿信息及型號;3D視覺系統將砂芯型號發送給機器人,機器人切換相應夾具。
·?3D視覺系統引導機器人抓取砂芯進行浸涂處理(砂芯浸涂工位)。
·?3D視覺系統引導機器人鉆孔、抓取上蓋芯安裝于下蓋芯(砂芯鉆孔、組芯工位)。
·?3D視覺系統引導機器人抓取砂芯放置于下料臺(砂芯下料工位)。
02?方案優勢
高性能3D視覺系統,實現高效、高質量生產
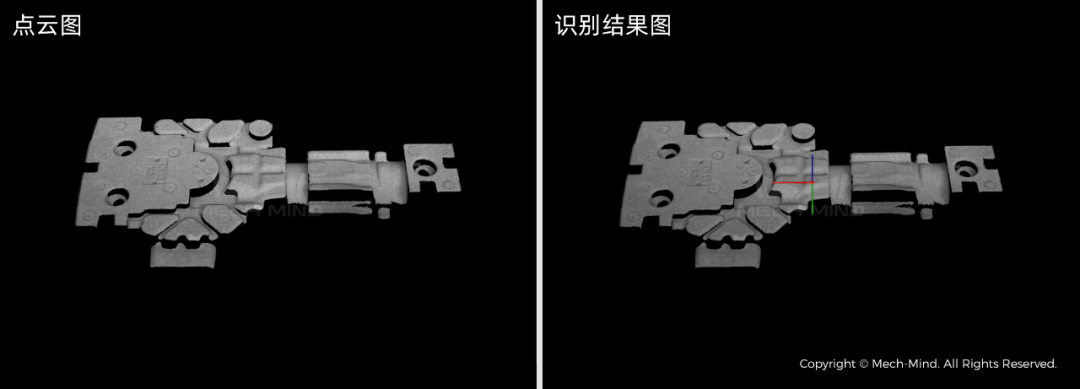
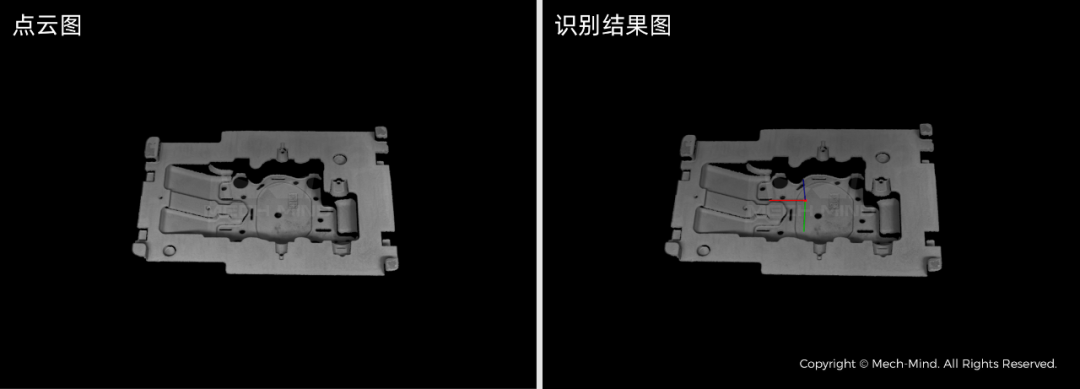

從上至下依次為機體芯、上蓋芯、下蓋芯
·?現場選用了Mech-Eye PRO S高精度結構光工業3D相機。Mech-Eye PRO S能夠輕松應對現場不同工位、不同時段的環境光干擾,對表面凹凸不平、帶有字符&特征孔的各類砂芯生成高質量點云數據。
·?Mech-Eye PRO S臂載式安裝,視野更靈活,輕松覆蓋到位不一致的砂芯。成像速度快,實現砂芯抓取位姿的快速反饋。
·?3D視覺系統精準定位上下蓋芯,引導機器人依照砂芯復雜裝配特征完成高精度組芯工藝。
先進AI技術,助力客戶產線穩定運行
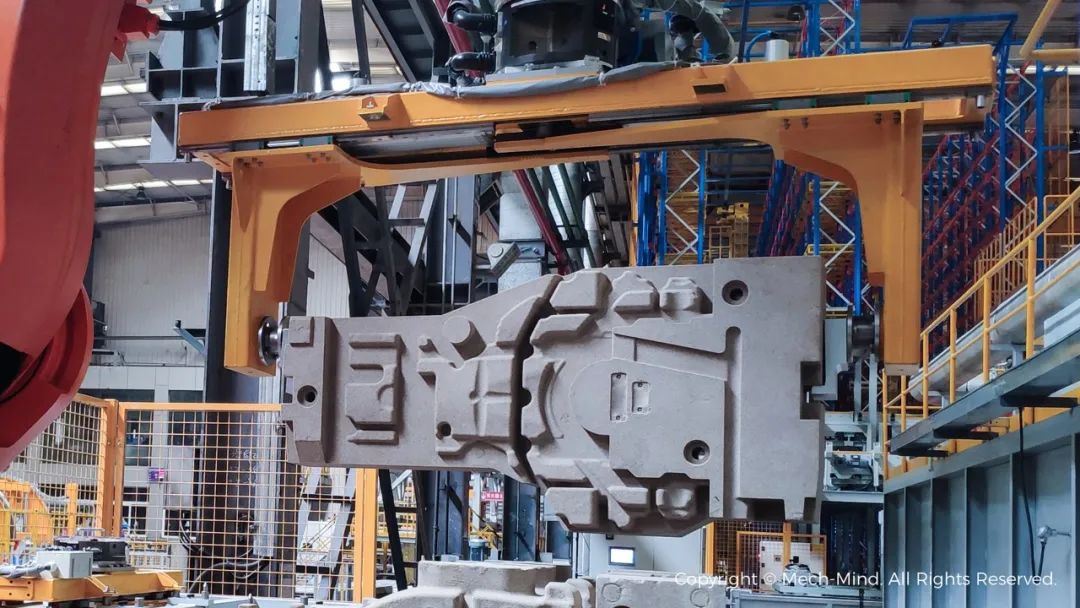
精準抓取
·?現場布局緊湊,集成了機器人、輸送線、浸涂池等各類工業設備。自研機器人運動路徑規劃技術,結合運動仿真+碰撞檢測,輕松應對現場復雜工況,高效聯動各個工藝流程。
·?3D視覺系統準確識別砂芯尺寸,提前調節夾具行程,保證均勻浸涂、精準鉆孔及對位組裝。
·?可根據訂單需求處理現場數十種砂芯,同時支持新增產品的快速導入。
生產效率大幅提升,鑄件質量有保證
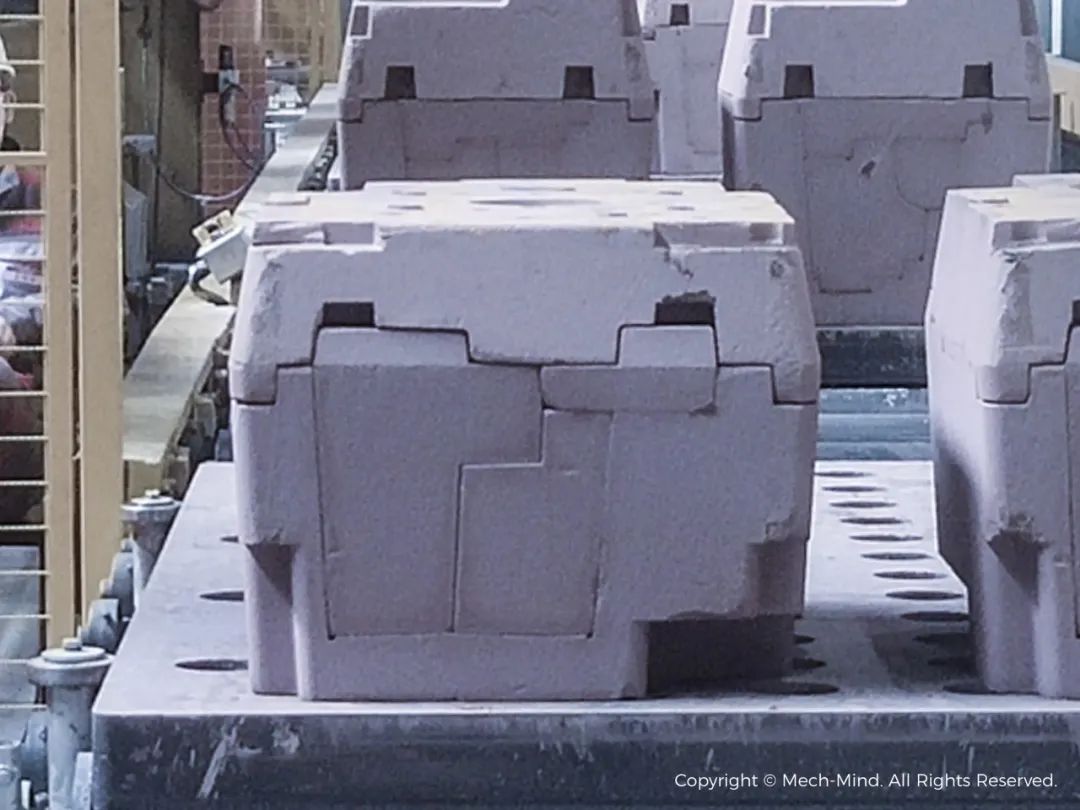
砂芯裝配成品
·?通過AI+3D視覺+工業機器人解決方案,將勞動密集型作業轉化為高度自動化作業,整條砂芯生產線效率提升至原來的2倍。
·?通過3D視覺技術實現砂芯高精度定位,無需頻繁切換定位工裝,提升產線柔性。
·?砂芯表面涂料覆蓋均勻、氣孔準確且具有一致性、對位組裝更為精準,保證復雜鑄件精度滿足客戶出廠需求。
梅卡曼德通過3000+案例交付積累了豐富的應用經驗,在全球范圍內率先實現了AI+工業機器人多應用、跨場景的批量落地。助力合作伙伴更便捷、更快速地為終端客戶交付各類復雜機器人應用。如果您想了解更多梅卡曼德產品及方案,請發送郵件至info@mech-mind.net。